Plastic Forming
For more information select the headings below for more information
Welding
There are many types of welding in the plastics industry but at Victory we feel that using Infrared has great advantages, especially for the welding of plastic pipes.
IR welding is a non-contact heating technique to melt and then fuse thermoplastic parts together using the energy from Infrared radiation.
IR welding typically uses a range of wavelengths from 800 – 1100nm to heat, melt and fuse the interface between two plastic parts through the absorption and conversion of the IR energy into heat.
IR welding is a much faster and more controllable than alternative options of plastic welding.
Various IR emitters can be used and developed for your exact requirement. It can represent a cost saving and more productivity due to the fast nature of the process which is desirable for all in the industry.
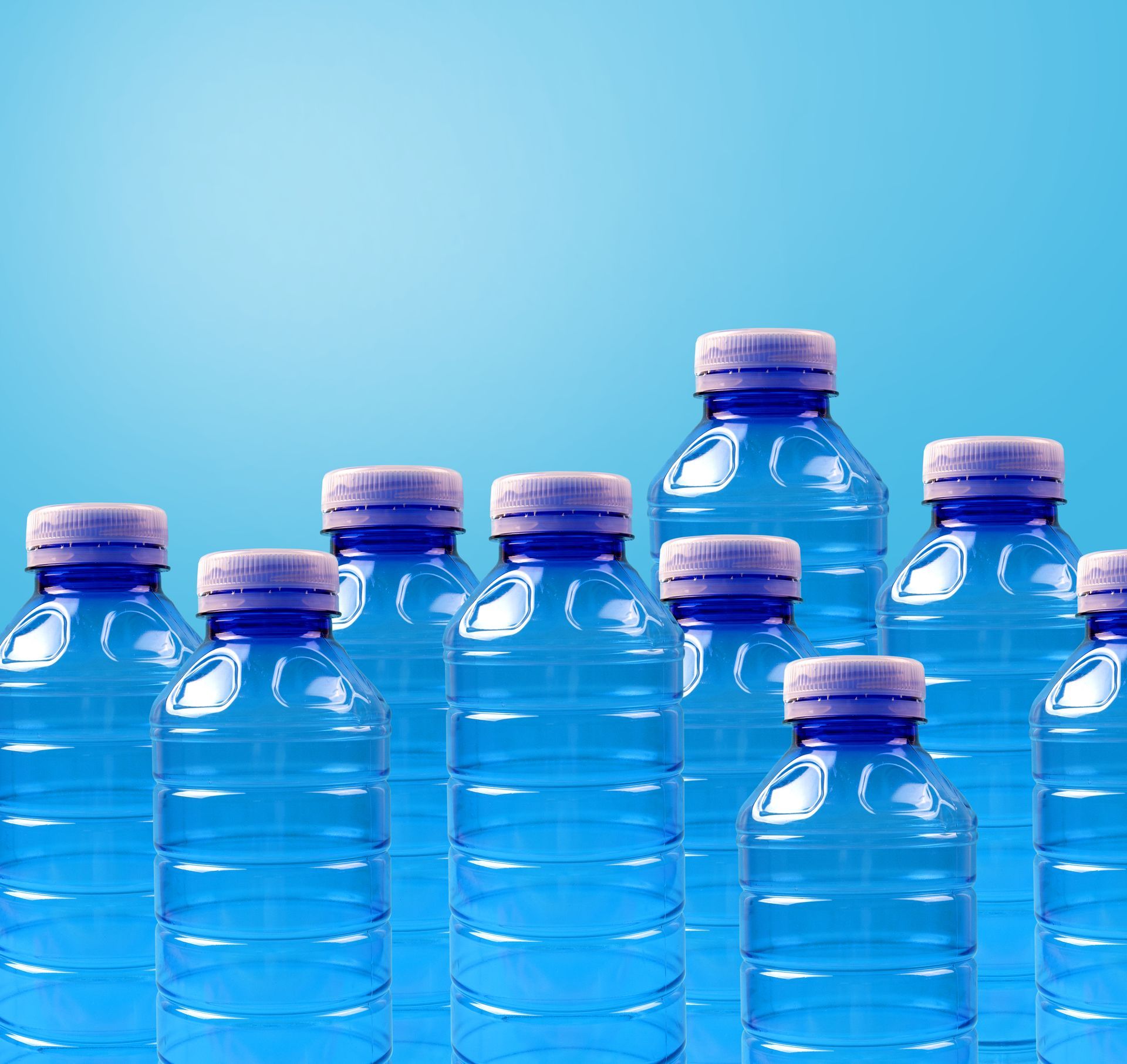
Bottle Manufacturing
Manufacturers are looking for heat processes that are easy to control and provide instant heat.
Using infrared systems that use the correct controllers for the application, will meet this requirement.
How does infrared work!
IR lamps transmit infrared electromagnetic waves which create heat when they are absorbed by objects.
In this way, the infrared emitter does not have to be in direct contact with your product and can be placed a suitable distance away while still providing the heat required for your applications.
These infrared waves are not affected by airflow, therefore a consistent level of heat is maintained regardless of external factors in the location of your machinery.
Each material substrate has its own absorption spectrum, this means that only the infrared at the correct wavelength is absorbed while incorrect wavelengths are either reflected back or pass straight through the substrate.
Our Technical Department will work with you to ensure that the emitters we provide have the correct wavelength for the materials in your product to give the optimal heating requirement.
Infrared has the following benefits: - instant heat, more controllable, cheaper to run , are affected less by external factors
Thermoforming
Thermoforming is the process of heating plastics to form into specific shapes.
Infrared heating is a great tool to use in this process, especially IR lamps and IR ceramic emitters.
Quartz Infrared heating gives a rapid response and high efficiency resulting in time and energy savings while thermoforming in specialist plastics production.
Vacuum forming thermoforming uses an IR source to produce a perfectly formed plastic container to fit your exact requirement.