An example from the construction of a new process line for an automotive factory (Ford in Romania). This has helped reduce the cost and energy consumption of the process while at the same time reduced the line length by over 60m. A process that used to take 20 minutes to complete is now performed in 3 minutes (only the heating stage is shown here on the demonstration unit).
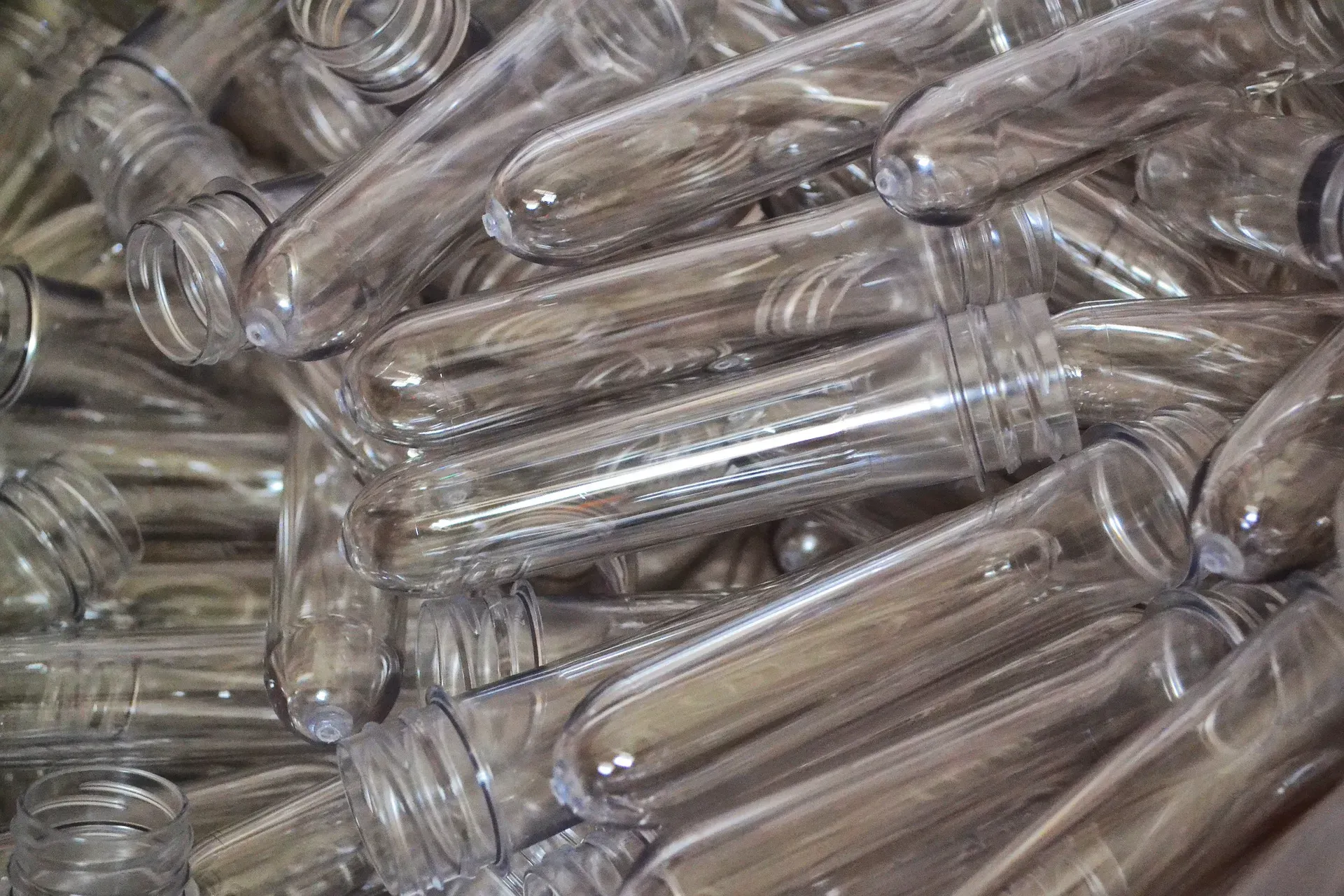
We work with many factories and manufacturing facilities to help improve their production processes.
Blow Moulding Technologies in Northern Ireland contacted us with the objective of reducing their energy costs during the process of manufacturing PET plastic bottles.
The PET preforms must undergo a heating process before they are blow moulded into the exact bottle shape, this can be time consuming but also very expensive.
After various tests and experiments at our UK R&D facility we determined that a much more energy efficient way of carrying out the preform heating process is the use of reflector coated short-wave Infrared heating module.
Standard IR lamps are clear, and the heat is emitted all around itself, the use of a 180-degree internal reflector allows the heat to be directionally targeted towards the preform meaning that more infrared is absorbed by the PET material than their current system.
As a result of this we were able to reduce the wattage of the IR lamp they were currently using which gave an increased performance but reduced energy consumption by 20-25%.
A major automotive supplier required a change in its manufacturing process which involved heating of an adhesive to over 100℃ in a matter of seconds but not to exceed 5 degrees higher. It also needed to interface with a rapid switching system triggered by a robot.
Victory analysed the material to be heated and found that shortwave IR emitters in a special formation produced excellent results. We also produced a control system with soft start and interface with the robot system.
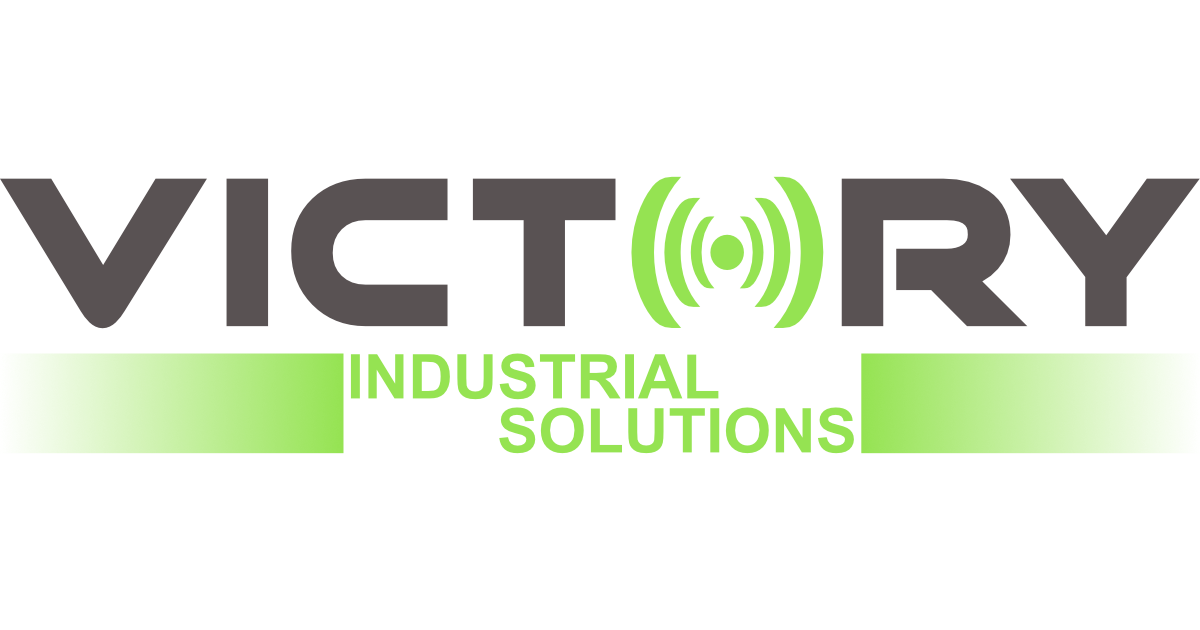